MOOC List is learner-supported. When you buy through links on our site, we may earn an affiliate commission.
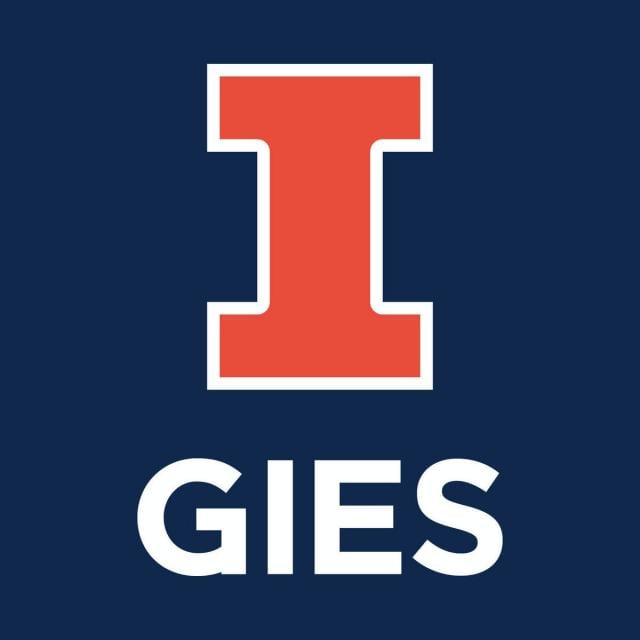
MOOC List is learner-supported. When you buy through links on our site, we may earn an affiliate commission.
Upon successful completion of this course, you will be able to:
• Understand the role of operations management
• Relate underlying principles to operations management frameworks and techniques
• Synthesize information to make strategic operations decisions
• Evaluate processes on different dimensions
• Apply analytical techniques for tactical operations decision
Course 3 of 7 in the Value Chain Management Specialization.
Syllabus
WEEK 1
Course Orientation & Process Analysis
In this module, you will be introduced to the idea of operations as processes that are composed of coordinated activities. Processes will then be characterized by how activities and resources required to perform them are organized. Process types will be described and guidelines on the appropriate choice of a process type will be presented. Activities and processes will be analyzed and key performance metrics will be presented. You will learn about cycle times, flow rates, throughput times, and how to calculate them for activities and processes. The calculated metrics will allow you to identify bottleneck activities and understand the idea of capacity utilization. The module ends with Little’s law, which introduces the notion of inventories and how other process metrics are related to amount of inventory in a process.
WEEK 2
Inventory management
In this module, you will learn the importance of inventory management, and effective ways to manage inventories. We will explore different types of inventories and why organizations maintain inventories. You will learn about macro-level inventory performance measures, as well as the various drivers that affect the amount of inventory. You will learn how inventories are managed, how much should be ordered and when. You will learn analytical models, such as the Economic Order Quantity and Economic Manufacturing Quantity, that optimize the order or manufacturing quantities to minimize cost. The effects of lead times and demand variability on inventory management decisions will be discussed and you will learn to calculate safety stocks and re-order points.
WEEK 3
Supply Chain
In this module we explore supply chains and discuss some of the important considerations associated with supply chain management. Using the example of coffee, we discuss the complexities associated with the design and management of supply chains. You will learn about issues arising from sourcing materials, logistics of moving and storing material, and information that is needed to manage the supply chain. You will also understand governance issues and the use of contracts, sustainability of supply chains, and the risks inherent in the workings of a supply chain. Because the sourcing of materials is a major function in supply chain management, you will learn about make-or-buy decisions and the theory of transaction cost economics that undergirds such decisions. Finally, you will learn about the bullwhip effect which explains the magnification of demand variability in a supply chain and the role of information in mitigating this problem.
WEEK 4
Continuous improvement
This module begins with a brief introduction to the pioneering work of W. Edward Deming’s contribution. You will understand Deming’s chain reaction, system of profound knowledge, and the PDCA cycle. Major developments in the CI movement (Lean management, Six-Sigma, TQM, Business Process Re-engineering, and Theory of constraints) that were spawned by Deming’s work are discussed. We will then do a deep dive into two of these initiatives - Lean management, also known as the Toyota Production System, and the Six-sigma methodology. In Lean management we will explain value-adding and non-value-adding activities and the different types of waste. You will learn about Lean management tools such as 5S, 5-Why, Kaizen, and Value Stream Mapping. In Six-sigma you will understand the origin and implications of the six-sigma quality standard. You will learn about the DMAIC framework and the SIPOC process to identify problem areas, and the infrastructure that is required to fully implement six-sigma methodologies in an organization.
MOOC List is learner-supported. When you buy through links on our site, we may earn an affiliate commission.
MOOC List is learner-supported. When you buy through links on our site, we may earn an affiliate commission.